高向洲1 于恒亮1 王默楠1 罗果萍2 (1.包头钢铁(集团)公司 炼铁厂;2.内蒙古科技大学)
摘 要 本文主要围绕 1号高炉能耗较高的情况进行研究,对于入炉料的冶金性能通过实验测定,对其数据进行分析并找到合适的炉料结构优化方向及途径,综合炉料中包钢使用的澳大利亚块矿与包钢球团矿互换,对其综合炉料的软熔性能影响不大,为提高高炉入炉料的质量,进一步实现节能降耗目的提供有效依据,明确当前高炉节能降耗的理想炉料结构为占比75%烧结矿和占比25%球团矿。 关键词 节能降耗 冶金性能 炉料结构
高炉炼铁的低燃料比数值是世界钢铁行业不断追求的目标,相关统计显示[1],欧洲当前的高炉总燃料比值仅仅在440kg/t~460kg/t之间,而当前最新的焦比指标为300kg/t,高炉煤比值超过200kg/t,其中数值最高的是CORUS 6号以及7号高炉,由于自身的利用系数较高,在连续两年的时间内保持在225kg/t~230kg/t的范围,包钢1号高炉目前燃料比偏高,优化炉料结构势在必行。 1 高炉入炉原、燃料现状 1号高炉第一组综合入炉料的结构为75%的高碱度烧结矿,占比5%的澳矿以及占比20%的酸球团矿,第二组高炉综合入炉料的结构为70%的高碱度烧结矿和占比30%的酸球团矿,第三组高炉综合入炉料的结构为75%的高碱度烧结矿和占比25%的酸球团矿,其中烧结矿主要来自于厂区内的两个烧结区域当中,按照现有入炉料结构以及厂区球团的生产能力,用于生产的20%的球团需要外购,但是外购矿的成分以及冶金性能变化较大,并不利于高炉稳定生产,为了确保设备水平较为先进的1号高炉可以稳定生产,所以自产的球团矿应该先供给高炉使用,按照当前厂区自产焦炭的情况,其中 70%的入炉焦炭需要采用外购的形式,而块矿主要选用澳矿,配比1,配比2,配比3所使用的球团矿,烧结矿,喷吹煤粉以及焦炭等其性能与成分组成如下表所示。 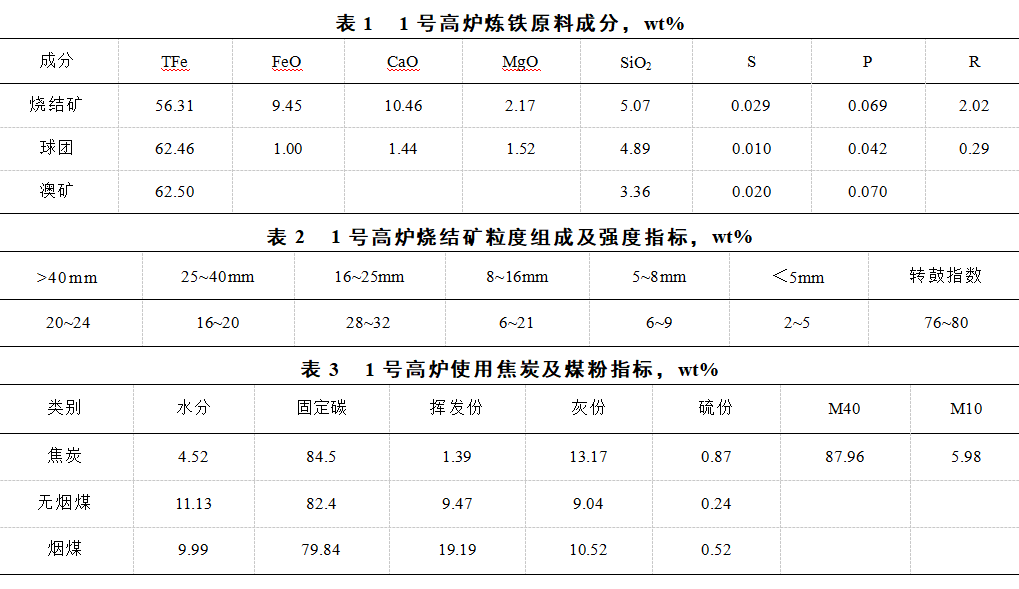
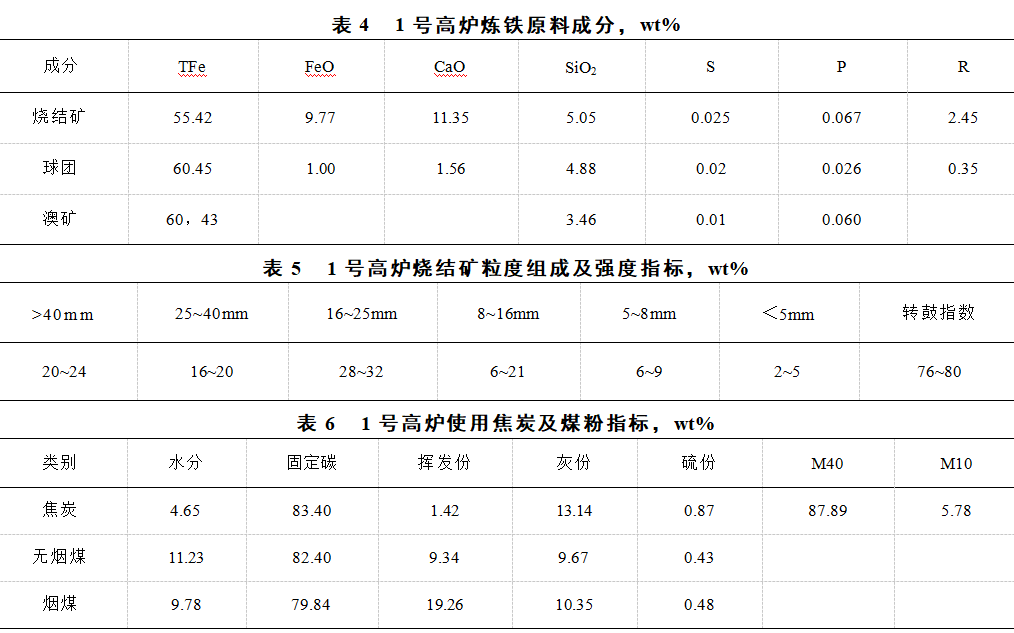

2 炉料冶金性能的测定 2.1 炉料的冶金性能对高炉能耗及生产的影响 炉料的冶金性能对高炉的生产、能耗以及产量等指标具有直接性的影响,通过对炉料成分以及冶金性能的分析以及国内外炉料指标的比对数据可以找出炉料冶金性能的改进方向,这对于炉料结构的优化以及高炉精料技术的实现提供了一定的理论基础,对于高炉的节能降耗具有重要意义。 2.2 冶金性能测定方法 还原性能是指衡量还原性气体将铁矿石中相结合的氧进行排除的难以程度的量值,这是一项较为重要的高温冶金 性能指标,参照我国当前国家标准GB/T13241-91“铁矿石还原性的测定方法”,目前宝钢所引用的是日本先进的 JIS 测定方法,这两种测定法的结果如表 10所示。 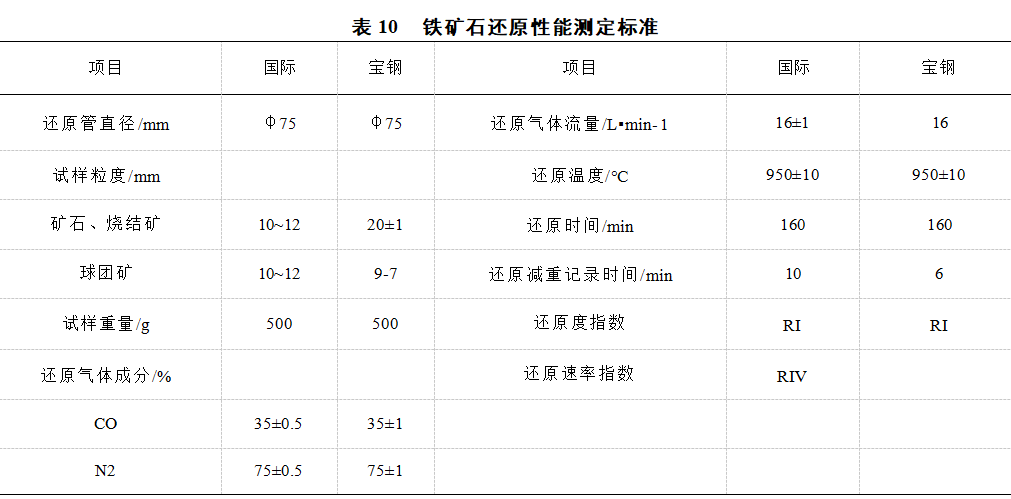
低温还原粉化性能在烧结矿中的冶金性能中至关重要。还原粉化率的测定方法主要分静态方法和动态方法,目前宝钢采用的静态法,方法引进主要来源来自于日本和德国,其两种方法如下表 11所示。 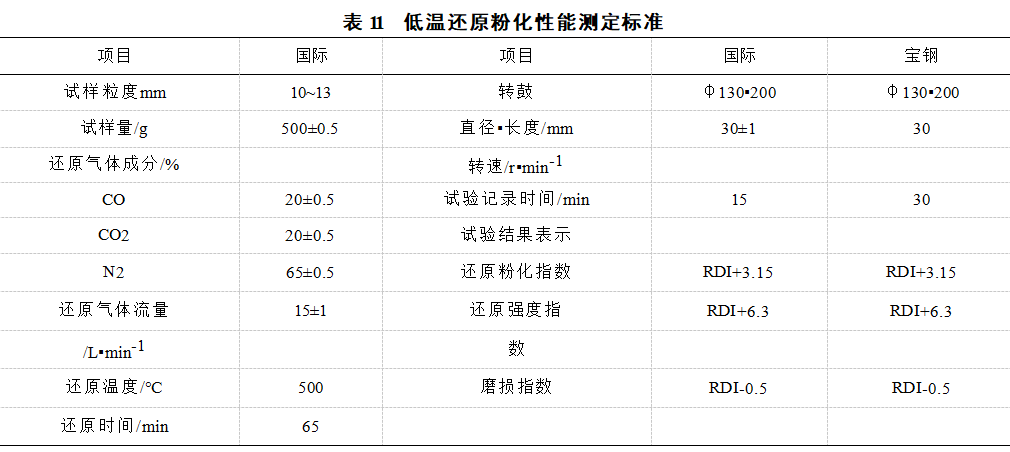
炉料的荷重软化性能和滴熔性能的测定主要使用德国研究协会的 BFB 设备以及日本的测定方法,目前我国尚且没有统一的标准,应用较多的是北京科技大学所设定的方法。 2.3 实验内容及方法 (1)实验内容。文中实验主要测定 1号高炉不同配比的炉料结构中自产烧结矿,球团矿以及入炉综合料,进口澳矿的冶金性能,测定内容为低温条件下的还原粉化性能以及中温条件下的还原性。(2)实验仪器。本次实验过程中所使用的仪器主要包括有东北大学自行研制的铁矿石,焦炭冶金性能的测定仪,铁矿石在高温条件下软熔滴落的测定仪以及煤气发生炉,各种直径型号下的标准检验筛和天平等。(3)实验方法。本次实验对炼铁原料的还原性以及低温条件下的还原粉化性测定按照相关标准进行测定,荷重软化以及熔融滴落性测定采用东北大学的相关方法,1号高炉炼铁炉具体内容如下表所示。 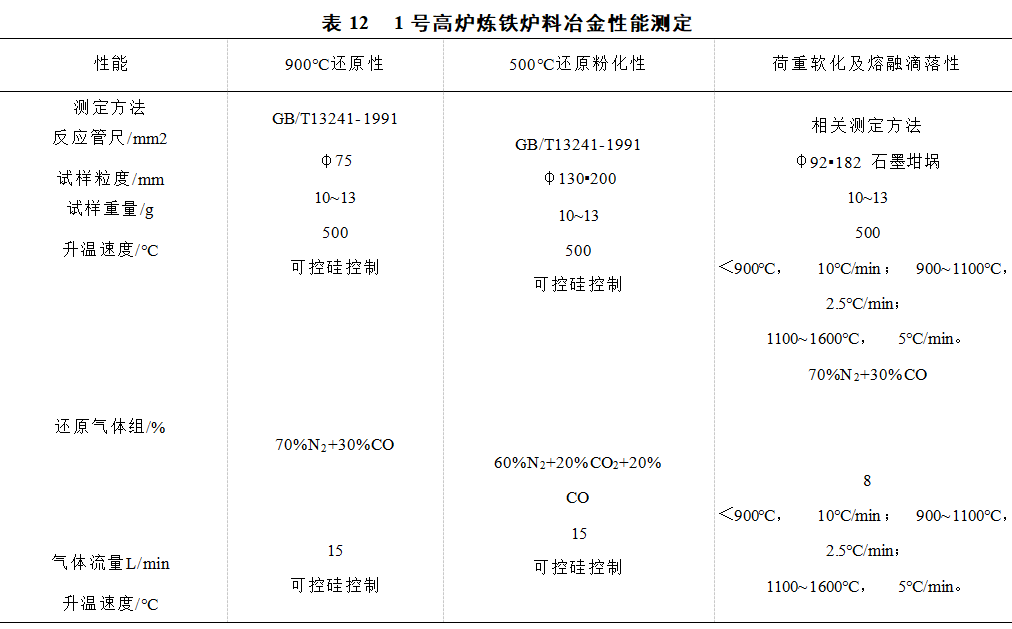
(1)实验测定补充内容。①本次实验当中所采用的测定方法为铁矿石还原性测定法,它是对入炉料还原性进行评价的重要指标,还原度的评价指标采用“RI”进行表示,一般认定指标 RI<60%,炉料本身的还原性较差,如果RI的数值>80%,则其还原性较为优良,还原性RI的计算公式如下所示:RI=[0.11B/0.43A+(m1-mι)/0.43A▪M0▪100%] (式 3-1)A、B分别是式样当中的TFe和FeO的含量(%),其中M0为式样质量(g),m1以及m2分别为开始进行还原以及还原t分钟之后的式样质量(g)。参考指标可以选用“RVⅠ”表示,RVⅠ代表以三价铁为基准状态,当还原度达到40%时的还原速率,采用重量百分数每分钟进行表示,其中参考指标RVⅠ的计算公式如下所示。RVⅠ=dRt/d(t0/Fe)=33.6/t60-t30 (式 3-2)t30—表示还原度达到30%时的时间,单位为min33.6—常数在特定条件下实验难以达到60%的还原度条件时,计算公式如下所示。RVⅠ=dRt/dt(0/Fe)=k/ty-t30(式 3-3)ty—代表还原度达到y时的时间,单位为min。K—取决于y的常数,在y数值为 50%时,其中k值为20.2,在y的数值为55%,K数值为26.5。②还原粉化性。本次实验采用铁矿石低温粉化实验静态法进行测定,在经过还原后产物通过转鼓进行筛分处理,同时得到低温还原强度指数RDI+6.3,低温条件下的还原粉化指数为RDI+3.15,低温条件下的还原磨损指数值为RDI-0.5。其中还原粉化指数为主要的考核目标,还原强度指数以及还原磨损指数为参考性的指标。其具体的计算公式如下所示:RDI+6.3 = md1/md2*100% (式 3-4)RDI+3.15 =md1 md2 / md 0*100% (式 3-5)RDI-0.5 =md0 md1 md2 md3 / md 0*100% (式3-6)在上式中,md0代表进行还原反应后试样的总质量,md1、md2以及md3分别代表粒度大于 6.3mm,在3.15mm到6.3mm之间以及0.5mm到3.15mm之间时试样的质量。③荷重软化以及滴熔性能。本次试验采用的是东北大学的测定方法,所测定的内容主要包括有软化开始及终结的温度,软化区间以及矿石开始熔化的温度,矿石熔滴温度以及软熔状态时的温度区间,在实验进行的过程当中参数分别采用T4、T40、T40-T4、Ts、TD以及TD-Ts、∆Pmax表示。 2.4 单一入炉矿料的性能结果测试分析 1号高炉单一入炉矿料中分别具有烧结矿,球团矿以及进口澳矿,三种矿石的化学成本以及冶金性能的测定结果分别如下表所示。 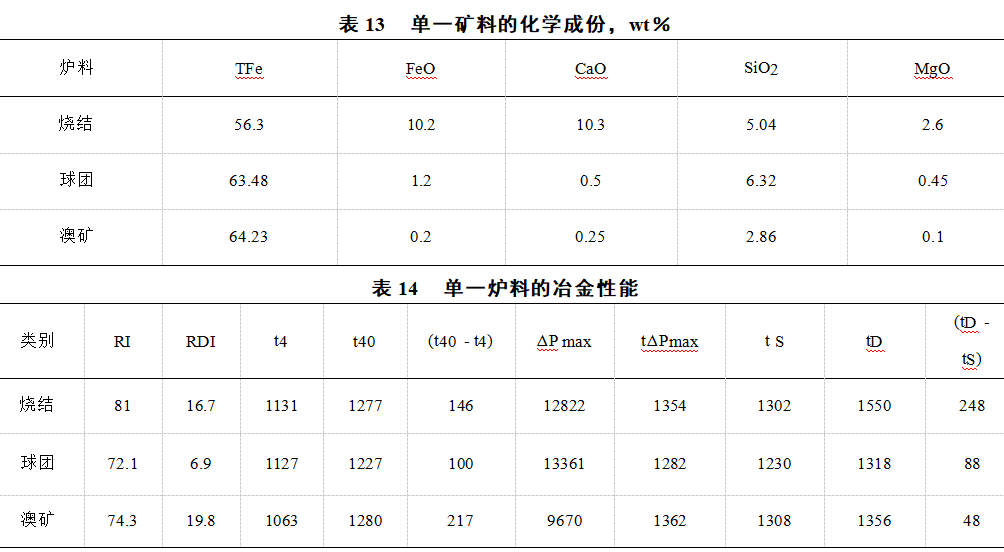
①根据 1号高炉入炉矿料冶金性能的测定结果进行分析,对不同矿料类型的还原性能,高温滴熔性能以及低温的粉化性能等进行对比。可以了解到对于单一矿料当中不同种类矿料的还原性能进行对比分析,烧结矿的还原性能最好,其次还原性能是澳矿,而球团矿的还原性能最次。入炉料当中还原性能的强弱与其中所含有的成分FeO和TFe有关,如果炉料当中TFe在炉料当中具有较高含量,而其中FeO的含量相对较低,则炉料当中所含有的具有较强还原性的赤铁矿含量较多,则其本身势必具有较好的还原性。从结构致密性的角度分析,较之于烧结矿而言,球团矿以及块矿的结构致密性更高,而块矿的结构致密度比球团矿更高,所以烧结矿的还原性能最好[2]。高炉当中所使用的单一炉料其低温还原的粉化性能指数RDI+3.15的大小依照其顺序具有最大值的为澳矿,其次为烧结矿,而球团矿的数值最小,由此可知澳矿的低温还原性能最为优良,最差的是球团矿,根据几种矿料的组成成分而言,还原粉化性能最好的是块矿,这是由于块矿当中 SiO2的含量较高,在进行焙烧的过程中内部的铁酸钙以及粘结相总量增加有关,这同时也会导致显微组织的均匀性增强,而球团矿本身的还原粉化性能较差是由于其中的FeO含量相对较低而TFe的含量相对较高导致,同时由于其成分当中的FeO的含量相对较低,这也就导致了Fe2O3具有较高含量,在进行低温还原的过程当中,较之于其他的炉料而言Fe2O3与还原性气体的接触较多,这主要是由于内部的晶型发生变化从而产生较为严重的粉化现象导致。通过上述分析可以了解到,高炉冶炼过程中所使用的烧结矿与球团矿和澳矿相比,其还原性能以及低温粉化性能更为优良,具有更高的熔滴温度以及软化开始温度,其拥有更好的性能,荷重软化以及高温的熔滴性能球团矿就要显得更为优良,但其的低温粉化性较差,块矿虽然具有良好的低温粉化性能但其还原性能以及软化性能较差[3]。 2.5 综合炉料中温还原性、低温还原粉化、熔融滴落测试结果 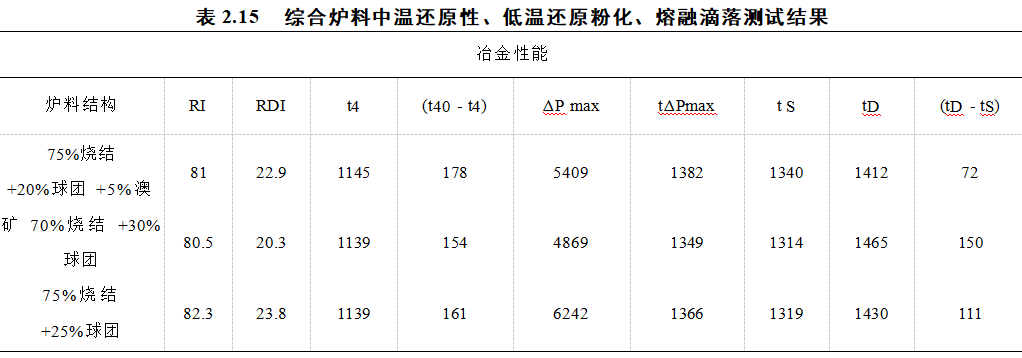
(1)通过测试得到的综合炉料的还原度和还原粉化指数与由单一炉料的还原度和还原粉化指数加 权推算出来的综合炉料的结果基本一致,差在10%以内。(2)以上3种综合炉料的软熔滴落性能与组成它们的单一炉料相比, 其最大压差明显降低,熔融滴落区间明显变窄。各软化特性温度(t4和t40 )均有不同程度的优化。(3)综合炉料中包钢使用的澳大利亚块矿与包钢球团矿互换, 对其综合炉料的软熔性能影响不大,优化调整炉料结构时,应充分考虑其价格因素。 3 综合炉料优势 1号高炉所使用的入炉原料包括有烧结矿,球团矿,进口澳矿,不同入炉原料具有各自的优劣性能。1号高炉所使用的综合性入炉料冶金性能较好,和之前的单一入炉料相比具有明显改善,采用当前入炉矿料后焦比含量为400kg/t左右,虽然与国内先进的高炉炼铁的焦比仍然存在一定的差距,但是在一定程度上反应了1号高炉的节能优势,采用当前入炉矿后煤比值为165kg/t,基本已经达到国内先进高炉的煤比数值,降低焦比值提升煤比值有利于提高Fe的间接还原反应,从而减少直接还原反应的发生,不但可以减少焦炭等固体燃料的用量,同时也有效提升了碳素的利用效率。 4 结论 (1)综合炉料的还原度和还原粉化指数与由单一炉料的还原度和还原粉化指数加权推算出来的综合炉料的结果基本一致,差在10%以内。(2)当前高炉节能降耗的理想炉料结构为占比75%烧结矿和占比25%球团矿。(3)综合炉料中包钢使用的澳大利亚块矿与球团矿互换,对其综合炉料的软熔性能影响不大, 优化调整炉料结构时,应充分考虑其价格因素。
5 参考文献 [1] 毕雪亮.高炉添加块矿对炼铁过程的影响[D].华北理工大学,2017. [2] 董绍宾.唐钢烧结配矿及工艺条件优化研究[D].河北理工大学,2007. [3] 周传典.高炉炼铁生产技术手册[M].北京:冶金工业出版社,2005.
(责任编辑:zgltw) |